Peristaltic Metering Pumps Explained, Facts, Function and the Right Applications
Roller, hose, or tube pumps, also known as Peristaltic Metering Pumps, now boast enhanced capabilities thanks to technological and design improvements.
The peristaltic pump was first patented in the U.S. by Rufus Porter and J. D. Bradley in 1855 (U.S. Patent number 12753). So, not only has peristaltic pump technology been around for a long time, but history shows it can also be used in many diverse applications.
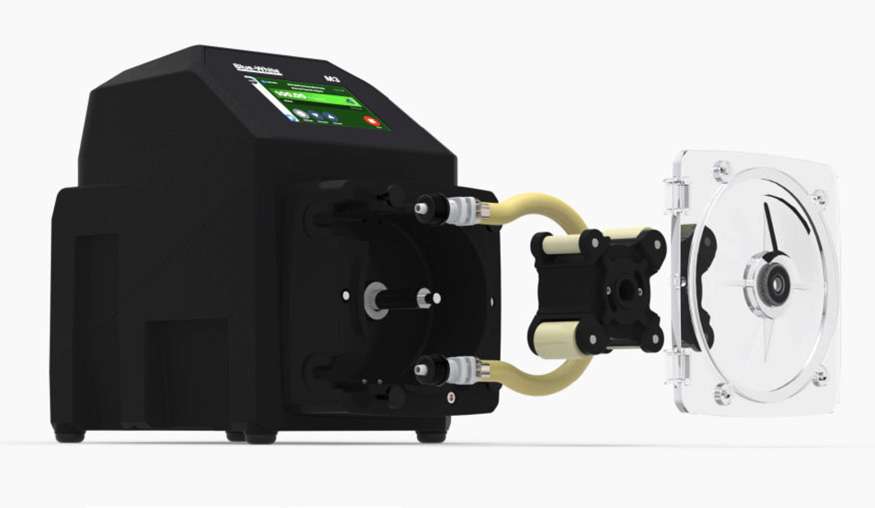
Peristaltic Metering Pumps, which are also referred to as roller pumps, hose pumps or tube pumps, are a type of positive displacement pump. Although they may operate today in a similar manner as they traditionally have, advancements in technology, enhanced design features, and highly functioning materials have significantly improved the capabilities and operation of peristaltic pumps.
How do peristaltic pumps work? The simple answer is, these pumps operate using a set of rollers which compress and release a flexible tube or hose, creating a smooth peristaltic motion that gently moves fluids through the pump tube without damage.
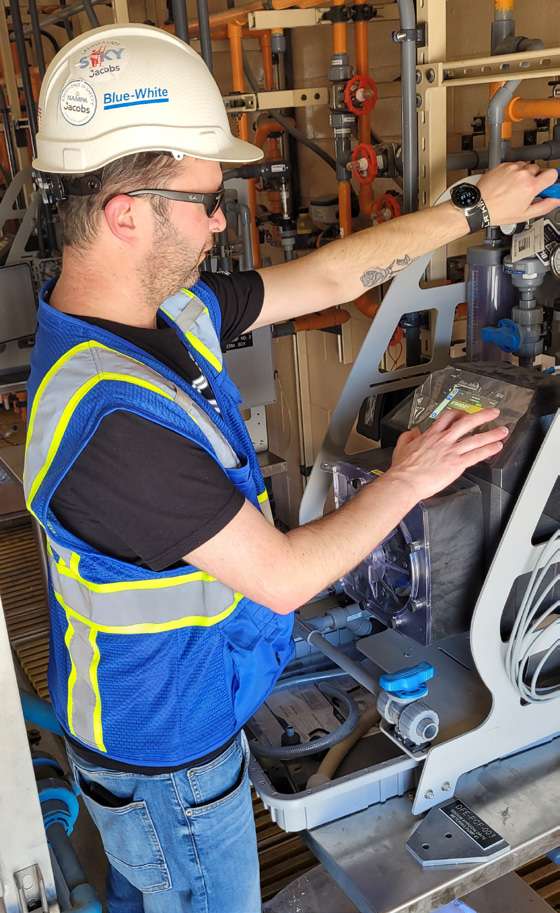
What are some common uses of peristaltic pumps? Peristaltic pumps are a popular option for dispensing chemical for the treatment of both industrial and public water and wastewater/effluent.
Chemical disinfection and sanitizing are often achieved using Sodium Hypochlorite, (Chlorine), or PAA, (Peracetic Acid). These chemicals are familiar to operators, but they do bring challenges. Both chemicals are off gassing however, peristaltic pumps are extremely effective when dosing fluids that contain trapped gases because they are not affected by air bubbles… bubbles simply pass through the tube. There is no vapour lock and no loss of prime.
Peristaltic pumps excel at pumping delicate chemicals like polymers. These high viscosity fluids are used for Flocculation and Coagulation to aid in the removal of solid particles. The smooth, gentle pumping action of peristaltic metering pumps like Blue-White®’s FLEXFLO M4 makes these pumps the preferred choice when dosing long chain polymers because the pumping action won’t cause damage to them.
Other common applications where Peristaltic Pumps are used include dispensing food and beverage flavourings, colourings and other additives. They’re an excellent choice for dosing descalers and other chemicals for cooling tower and boiler water treatment. They are used to dose vitamins and nutrients in farming and food production. In the car wash industry, peristaltic pumps are used to inject soaps, waxes and degreasers into car wash systems. That is to name just a few.
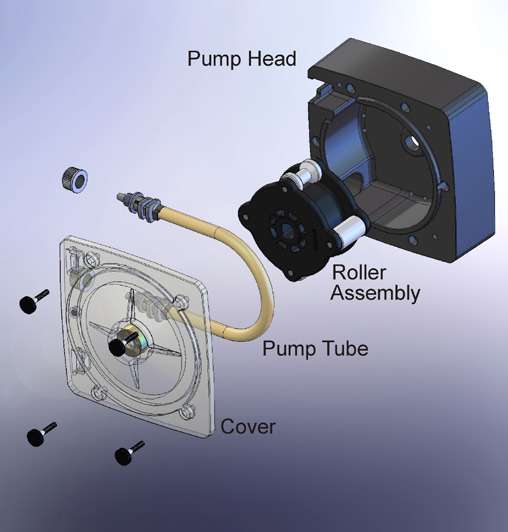
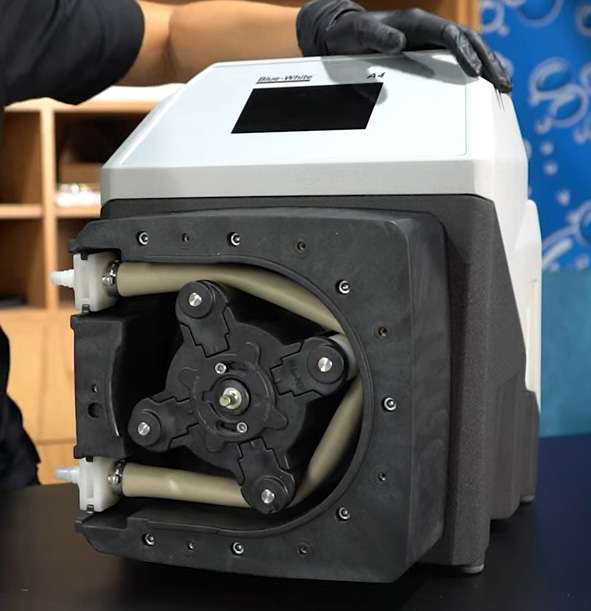
Depending on the material makeup of the pump tube, a peristaltic pump can handle a broad range of viscous, caustic and abrasive chemicals, as well as liquids with high solids content.
Checking for Material compatibility
It is important for peristaltic pump operators to choose a pump tube material that is compatible with the chemical being metered. Most manufacturers will list the materials that make up the pump’s wetted parts, enabling operators to determine the chemical compatibility of the fluid they are dispensing. In addition, manufacturers generally offer a range of tube material options and should have a compatibility chart available. Modern peristaltic pumps have many more tubing options available than in the past, meaning far better chemical resistance and increased tube life. It pays to do the research and discuss the challenges with the manufacturer in advance of installation and setup.
Correct Tubing Size
Larger orifice tubes can often be the simple solution when dosing highly viscous or abrasive fluids. The larger diameter makes it easier for thicker fluids to flow through the tube and reduces resistance against the tube walls.
Foot Valve
Operators may consider installing a foot valve in their metering setup, or use a pump that has a foot valve strainer already built in. This will help filter out excess particles in abrasive chemicals, and/or improve flow efficiency which is helpful for handling viscous fluids.
Tube Failure Detection
One of the most important advantages when choosing a peristaltic metering pump is the isolation of the chemical being dosed from the pump’s mechanical components. However, if the tube fails, this barrier could break down and cause damage to the pump mechanism, and other equipment if the leak goes undetected.
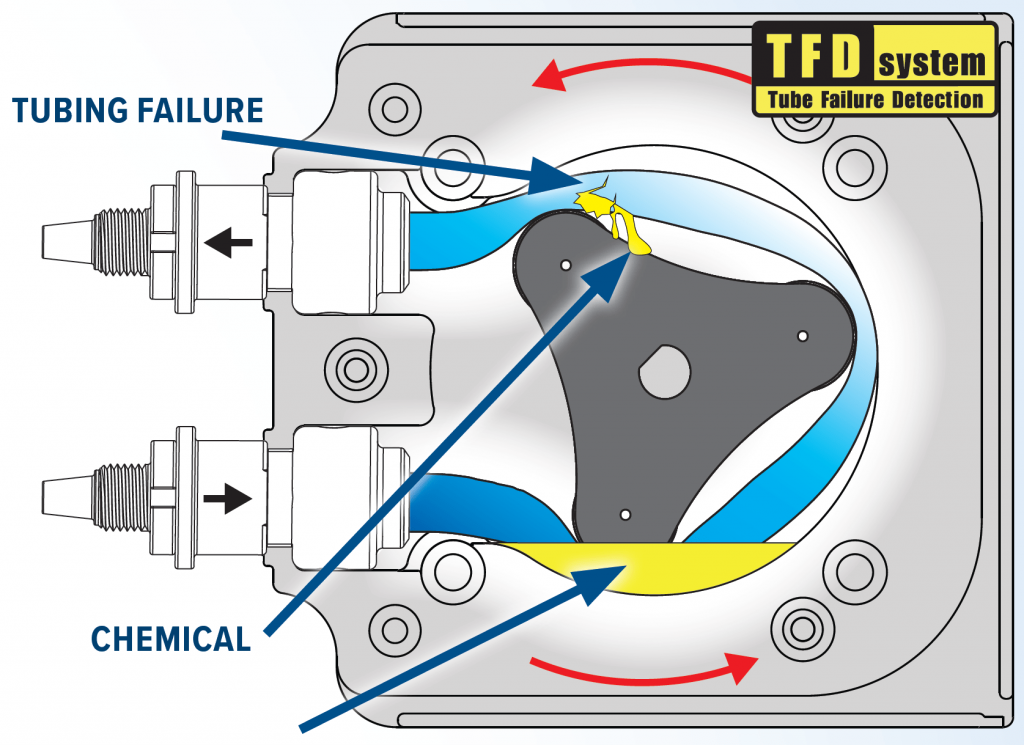
For this reason, quality peristaltic pumps are equipped with a built-in tube failure detection feature which stops the pumping action when leaked fluid is detected in the pump head. Blue- White’s patented TFD System detects a wide range of conductive chemicals with no false triggering. If the TFD detects tube failure, the pump will automatically shut off and energize a relay switch. This permits communication with external equipment, such as a back-up pump or alarm. Condensation and wash down procedures should not cause false triggering.
When peristaltic pumps are in use the pump operator must be aware that constant squeezing of the tube degrades it over time, slowly diminishing the feed rate. Most pump manufacturers rate tubes in hours so it’s important to know how many hours the pump has been running. Advanced peristaltic pumps will warn operators when it’s time to change the tube. When pump tubes are not regularly changed, or the injection point is not serviced, the pump tube may begin to leak.
The Benefits of Choosing Peristaltic Metering Pumps
Peristaltic pumps can be easier on operators because they are more “forgiving” than diaphragm metering pumps.
- Peristaltic pumps work well when there are high levels of particulate in the fluid being metered/dosed
- The gentle pumping action is favorable when metering delicate chemicals such as polymers
- Peristaltic pumps have no check valves to foul
- Due to strong suction lift, a peristaltic pump can be placed at a higher elevation than the chemical tank
- Peristaltic pumps will not vapour lock and will not lose prime
- Minimum maintenance is required. No special rebuild kits are needed
Peristaltic pumps may very well be the best choice for use in your application.